À l’ère où l’efficacité opérationnelle devient un levier essentiel de compétitivité, la méthode Kaizen s’impose comme une approche incontournable pour les entreprises cherchant à se transformer progressivement. Originaire du Japon, ce concept d’amélioration continue repose sur la mise en place de petits changements constants, impliquant tous les collaborateurs, du dirigeant aux équipes opérationnelles. En 2025, plusieurs grands noms tels que Toyota, Honda, Canon, et Panasonic continuent d’utiliser le Kaizen pour affiner leur production et renforcer leur position sur des marchés exigeants. Ce modèle, qui valorise la simplicité et la régularité plutôt que les révolutions technologiques, offre une voie pragmatique sur laquelle toutes les organisations peuvent s’appuyer pour relever leurs défis de performance. Cet article vous invite à découvrir les fondements du Kaizen, ses outils clés, et à travers des exemples concrets, à comprendre comment appliquer cette méthode pour booster votre efficacité au quotidien.
Les fondements historiques et philosophiques de la méthode Kaizen : une approche japonaise pour l’amélioration continue en 2025
Le concept de Kaizen, qui signifie « changement pour le meilleur », trouve ses racines dans le tissu industriel japonais d’après-guerre. À cette époque, le Japon faisait face à la nécessité de reconstruire une économie dévastée, en améliorant sans cesse ses process pour rivaliser avec les grandes puissances industrielles occidentales. Pionnier de cette méthode, le constructeur automobile Toyota a transformé ses lignes de production sous la houlette de Taiichi Ohno et Shigeo Shingo dans les années 1950, donnant naissance au Toyota Production System, reconnu mondialement pour sa rigueur et son efficacité.
Le principe clé de Kaizen découle d’une philosophie simple mais puissante : multiplier de petites améliorations régulières plutôt que d’attendre une révolution majeure. Cette démarche implique que chaque membre de l’organisation, indépendamment de son poste, participe activement à l’identification et à la résolution des problèmes. En 2025, cette philosophie représente un véritable levier stratégique pour les entreprises modernes, en particulier dans des secteurs technologiques aussi pointus que ceux investis par Canon, Sony et Mitsubishi, qui doivent constamment faire face à la pression pour innover tout en maîtrisant coûts et délais.
Plus qu’une simple méthode, Kaizen est aujourd’hui aussi considéré comme une culture d’entreprise. Son essence repose sur :
- L’élimination systématique des gaspillages et inefficacités
- La standardisation progressive des tâches
- L’engagement continu des collaborateurs dans un esprit collaboratif
- Le maintien d’une dynamique durable plutôt que des résultats ponctuels
Cette approche a été validée par de nombreux exemples à travers le monde, pas seulement dans l’industrie automobile, mais aussi dans des domaines variés tels que la santé ou les services financiers, où Hitachi et Shiseido intègrent ces principes pour améliorer la qualité de leurs services et l’expérience client.
Ce socle historique explique en grande partie pourquoi, en 2025, la méthode Kaizen demeure une méthode incontournable pour les entreprises cherchant à allier pragmatisme et performance durable.
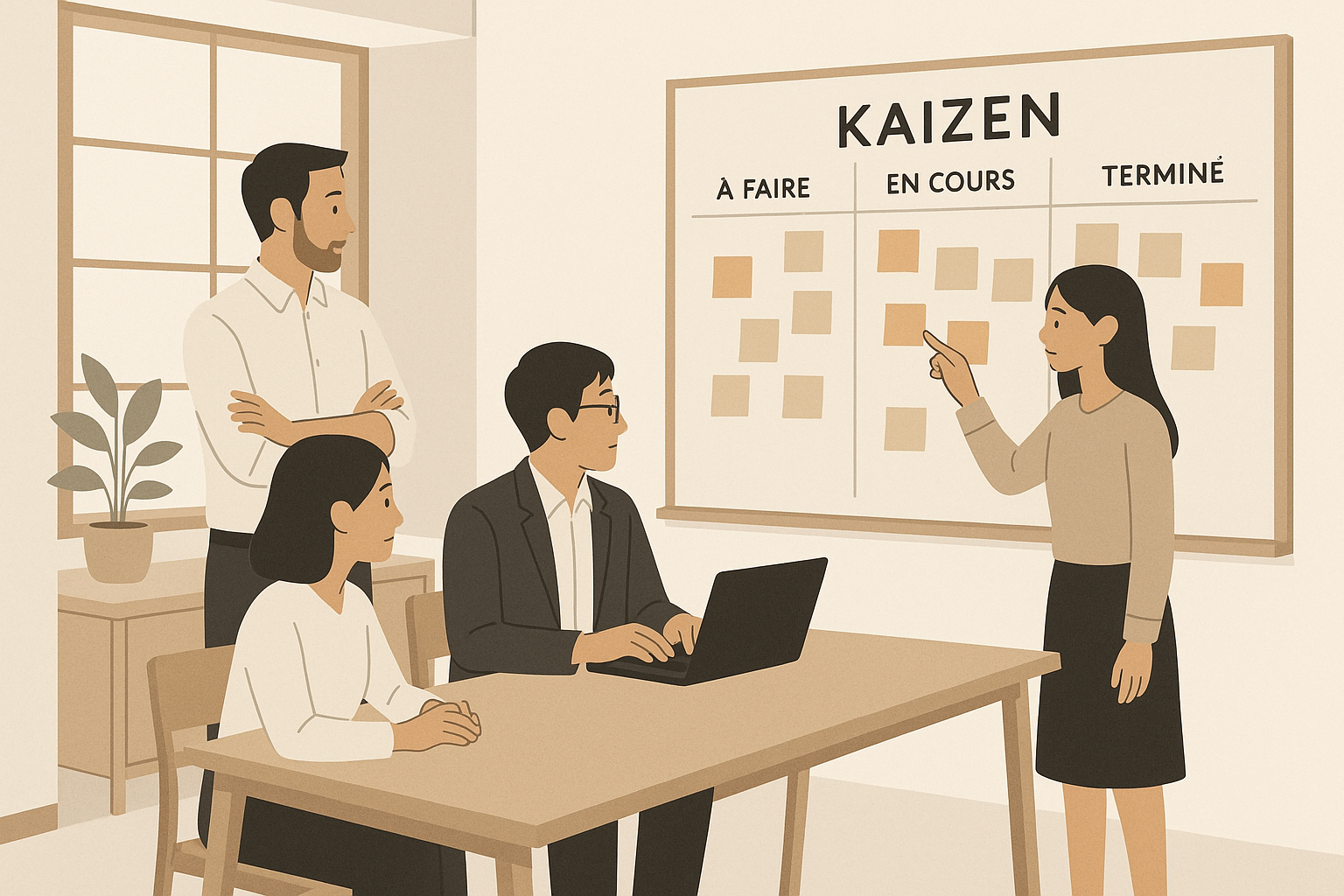
Les outils essentiels du Kaizen pour déployer une amélioration continue efficace dans votre organisation
L’efficacité de la méthode Kaizen repose sur un ensemble d’outils éprouvés qui facilitent l’identification rapide des problématiques et la mise en œuvre de solutions pragmatiques. En s’inspirant de pratiques traditionnelles et en les adaptant à l’industrie contemporaine, ces outils favorisent une culture d’amélioration accessible à tous.
Voici les principaux outils à maîtriser pour réussir votre démarche Kaizen :
- Les 5S : Cette méthode vise à organiser l’espace de travail de manière optimale. Chaque S correspond à une étape : Seiri (Trier), Seiton (Ranger), Seiso (Nettoyer), Seiketsu (Standardiser), et Shitsuke (Soutenir). Grâce aux 5S, les entreprises comme Nissan ou Mazda ont réussi à réduire significativement le temps perdu à chercher des outils ou matériaux, améliorant ainsi leur productivité.
- Le diagramme de Pareto : Fondé sur le principe des 80/20, ce graphique aide à concentrer les efforts sur les causes majeures des problèmes. Toyota l’a largement utilisé afin d’identifier que 20% des étapes du processus généraient 80% des défauts, focalisant ainsi ses améliorations de façon ciblée.
- Le diagramme d’Ishikawa ou diagramme en arête de poisson : idéal pour discerner les causes racines d’un problème complexe. En classifiant ces causes par catégories, ce modèle aide à éviter les solutions superficielles et incite à une réflexion approfondie.
- La boucle PDCA (Plan, Do, Check, Act) : Pilier central du Kaizen, ce cycle assure un suivi rigoureux des améliorations, en planifiant les actions, en mettant en œuvre les solutions, en contrôlant les résultats, puis en ajustant les procédures. C’est une méthode itérative qui garantit la pérennité des avancées.
Ces outils, bien que classiques, forment un arsenal puissant, en particulier lorsqu’ils sont intégrés dans un système de gestion qualité robuste. L’approche adoptée par des groupes comme Panasonic et Shiseido illustre parfaitement cette synergie entre outils Kaizen et objectifs stratégiques élevés.
Étapes concrètes pour mettre en œuvre avec succès la méthode Kaizen dans votre entreprise ou équipe
Déployer efficacement la méthode Kaizen nécessite une approche structurée et participative. Voici les étapes clés pour accompagner cette transformation :
- Analyser le processus existant : Réalisez un diagnostic précis des flux et identifiez les zones de dysfonctionnement. Cela peut passer par des observations terrain et la cartographie des processus.
- Identifier les problèmes : Utilisez des outils comme le diagramme d’Ishikawa pour comprendre les vrais facteurs bloquants. L’implication des équipes sur le terrain est indispensable à cette phase.
- Recueillir et prioriser les idées d’amélioration : Organisez des séances de brainstorming régulières où chaque collaborateur est invité à formuler des propositions. Utilisez une matrice d’Eisenhower pour classer les actions selon leur urgence et impact.
- Planifier les actions : Développez un plan détaillé avec des indicateurs de performance, des responsables clairement désignés, ainsi qu’un calendrier précis.
- Former les équipes : Offrez des formations adaptées, incluant des certifications Lean Six Sigma comme le Green Belt, pour renforcer les compétences nécessaires à l’amélioration continue.
- Mettre en œuvre et mesurer les résultats : Appliquez les solutions en veillant à un suivi rigoureux via la boucle PDCA. Utilisez des tableaux de bord et audits réguliers.
- Autonomiser et motiver les collaborateurs : Encouragez la prise d’initiative et le retour d’expérience. Valorisez les réussites afin d’entretenir la dynamique d’amélioration continue.
La réussite du Kaizen dépend fortement de la manière dont les managers et dirigeants soutiennent cette démarche, tout comme de la responsabilisation des collaborateurs. Lorsqu’elle est bien orchestrée, cette méthode permet des gains de productivité et de qualité durables, souvent visibles dès les premiers mois.
Études de cas emblématiques : comment Toyota, Honda et d’autres ont transformé leur efficacité grâce au Kaizen
La pratique du Kaizen est largement incarnée par des géants industriels japonais et s’est étendue dans de nombreux secteurs. Voici quelques exemples illustrant le potentiel de cette méthode :
- Toyota : Véritable pionnier, Toyota a intégré le Kaizen dès le milieu du 20e siècle, permettant notamment de réduire ses cycles de production de près de 50 % dans certaines usines. La qualité de ses véhicules s’en est trouvée significativement améliorée, consolidant la réputation du constructeur face à la concurrence mondiale. En 2025, Toyota continue d’être un leader en lean manufacturing grâce à l’application systématique de la méthode Kaizen dans toutes ses usines.
- Honda : Le groupe Honda a réussi à réduire ses rebuts de production de 20 % en deux ans grâce à des « cercles de qualité » où des équipes pluridisciplinaires collaborent pour proposer des améliorations continues. Cette dynamique a également favorisé une montée en compétences des collaborateurs via des formations Lean Sigma.
- Hitachi : Dans le secteur de la santé et des technologies, Hitachi a utilisé la méthode Kaizen pour optimiser ses processus internes et améliorer la satisfaction clients.
- Progressive Insurance : Non uniquement appliquée dans le secteur industriel, cette compagnie d’assurance américaine a adopté le Kaizen pour améliorer ses délais de réponse client de 40 %, tout en favorisant une meilleure implication de ses employés.
Ces exemples démontrent que le Kaizen transcende les frontières sectorielles et géographiques, s’imposant comme un outil adaptable aux exigences et réalités de chaque organisation.
Les impacts concrets du Kaizen sur la performance, les coûts et la satisfaction client
L’adoption de la méthode Kaizen se traduit par des bénéfices tangibles mesurables et durables. Les entreprises qui la mettent en œuvre remarquent généralement :
- Amélioration de la qualité : L’attention constante portée aux détails réduit les défauts, accroît la fiabilité des produits et services. Canon et Sony illustrent parfaitement cette progression dans le secteur technologique.
- Gain d’efficacité et réduction des temps de cycle : En éliminant les gaspillages et simplifiant les flux, les processus deviennent plus fluides. Les labo chaînes de Mitsubishi bénéficient de ces avancées.
- Diminution des coûts : La suppression d’activités inutiles et la rationalisation des ressources entraînent une baisse substantielle des coûts opérationnels, parfois jusqu’à 25 %.
- Hausse de la satisfaction client : Offrir systématiquement de meilleurs produits dans des délais raccourcis augmente la fidélité et l’image de marque.
- Renforcement de l’engagement des employés : Le Kaizen permet aux salariés de se sentir acteurs et écoutés, réduisant considérablement le turnover et améliorant le climat social.
Ces résultats encourageants font du Kaizen une méthode privilégiée pour les entreprises souhaitant conjuguer rentabilité et qualité durable en 2025.
Les principales résistances et défis rencontrés lors de l’adoption du Kaizen et comment les surmonter
Malgré ses avantages, l’intégration du Kaizen dans une organisation n’est pas sans obstacles. Plusieurs freins peuvent ralentir ou compromettre son adoption :
- Résistance au changement : Les employés craignent souvent que l’amélioration continue signifie davantage de travail ou une perte d’emploi. Une communication transparente et un management participatif sont essentiels pour gérer ces craintes.
- Manque de formation : Sans un enseignement clair des méthodes et des objectifs Kaizen, les équipes peuvent se sentir désorientées. Les certifications Lean Six Sigma sont souvent indispensables pour consolider la démarche.
- Culture organisationnelle rigide : Certaines structures, notamment dans des pays où la hiérarchie est rigoureusement ancrée, peinent à adopter ce modèle participatif. Dans ce cas, l’accompagnement par des experts en changement organisationnel est recommandé.
- Complexité perçue de la mise en œuvre : La nécessité d’un processus structuré DMAIC peut rebuter. Un pilotage adapté, avec un soutien au quotidien, aide à maintenir la dynamique.
En 2025, ces défis ne sont pas insurmontables à condition de les anticiper et de mettre en place les mesures adéquates. Le retour d’expérience des grandes entreprises comme Motorola ou Hitachi souligne l’importance d’une gouvernance claire et d’une culture de confiance pour réussir.
Le rôle fondamental de la culture d’entreprise dans la réussite et la pérennité du Kaizen
Le Kaizen ne s’arrête pas à la simple mise en place d’outils. Il est avant tout une transformation profonde du mode de pensée des organisations. La culture d’entreprise joue ainsi un rôle capital :
- Impliquer tous les niveaux hiérarchiques : De la direction aux opérateurs, chacun doit être partie prenante. À Toyota, cela signifie que même les employés sur la chaîne ont un droit de regard sur l’amélioration des procédés.
- Favoriser la formation continue : Les certifications Green Belt ou Black Belt facilitent la diffusion des bonnes pratiques Kaizen.
- Créer un environnement propice à l’innovation : Encourager les initiatives, accepter les erreurs comme des étapes vers l’amélioration continue.
- Valoriser les succès : Récompenser les idées qui ont eu un impact encourage les collaborateurs à s’impliquer davantage.
- Maintenir un esprit de collaboration : Le Kaizen repose sur la coopération interservices, essentielle pour détecter les gaspillages et proposer des solutions.
Chez des entreprises comme Sony ou Panasonic, cette culture est profondément ancrée, faisant du Kaizen un moteur puissant d’agilité organisationnelle et d’excellence opérationnelle.
Ressources et formations recommandées pour faciliter votre parcours Kaizen en 2025
Pour une adoption réussie de Kaizen, il est impératif d’investir dans des ressources pédagogiques solides et adaptées. En 2025, de nombreuses certifications et formations sont disponibles pour accompagner cette démarche :
- Formations Lean Six Sigma : Du Yellow Belt au Master Black Belt, ces programmes offrent une maîtrise progressive des outils Kaizen. Plusieurs centres, comme le Kaizen Institute ou le Lean Enterprise Institute, proposent ces cursus.
- Cours en ligne et MOOC : Des modules à distance permettent une initiation rapide et adaptée aux contraintes des entreprises et salariés.
- Ouvrages de référence : Les écrits de Taiichi Ohno et Shigeo Shingo, fondateurs du Toyota Production System, restent incontournables pour comprendre en profondeur la philosophie Kaizen.
- Consultants et experts : Collaborer avec des spécialistes permet de personnaliser la mise en œuvre selon la culture et les besoins spécifiques de chaque organisation.
- Financement par le CPF : En France, le Compte Personnel de Formation facilite l’accès aux formations qualifiantes, ce qui encourage salariés et demandeurs d’emploi à monter en compétences.
Finalement, la réussite du Kaizen dépend aussi de la capacité à intégrer ces apprentissages dans le quotidien opérationnel, en pilotant les projets avec rigueur et méthode. Un cadre bien défini contribuera à maximiser les retombées positives de cette démarche.